Während einer privaten Feier in der Sylvesternacht 1966 beschlossen wir, die beiden ASV‘er Hans Schlott (Schiffbau-Ing.) und Klaus Hannes (Verfahrenstechnik-Ing.), Schwertzugvögel zu bauen. Für jeden ein eigenes Schiff, das war unser Ziel. Vier Boote waren jedoch nötig, um mit dem Verkauf zweier Boote die eigenen zu finanzieren. Zu der Zeit waren wir beide Assistenten an der RWTH-Aachen. Damit standen uns das dortige technische Wissen und auch manche Hilfen, wie man hier sehen wird, bei unserem Vorhaben zur Verfügung. Die geplante „Serienfertigung“ führte zu der Entscheidung, die Boote nicht aus Sperrholz, sondern aus dem damals neuartigen glasfaserverstärkten Kunststoff (GFK) zu bauen.
GFK-Sandwichbauweise
Es gab am Rursee schon einen Eigenbau-Zugvogel aus GFK. Wir haben ihn uns angesehen. Für ein Regattaboot war die Vollpolyesterbauweise mit einer Masse von 350 kg, bei einer Vermessungsmindestmasse von damals 175 kg völlig ungeeignet. Von den Flugzeugbauern haben wir die Sandwichbauweise abgeschaut. Der geringere E-Modul des GFK wird durch Erhöhung des Widerstandsmomentes kompensiert.
Balsaholz als Zwischenlage war zu teuer und nicht feuchtebeständig. Geschlossenporiger PVC-Schaum war für uns die optimale Lösung, die wir nach vielen Versuchsreihen herausgefunden haben. Unsere damaligen Berechnungen zeigten, dass mit beanspruchungsgerechten Schichtdicken der äußeren und inneren GFK-Schichten mit einem 10 mm PVC- Schaumkern leicht 175 kg Masse für das fertige Boot erreichbar waren.
Werkstoffeigenschaften von GFK-Sandwichmaterialien
Da 1967 noch keine Daten über die Eigenschaften von GFK-Sandwich- konstruktionen verfügbar waren, mussten wir sie uns durch eigene Versuche im Institut für Textiltechnik und Werkstoffkunde selbst erarbeiten:
- Biegeversuche
- Biegewechselversuche
- Zugversuche in der Klimakammer
- Kerbschlagbiegeversuche
führten zur sicheren Auslegung des Sandwichaubaues für die verschiedenen Baugruppen des Bootes. „Salangan“ hat nach über 40 Jahren bewiesen, dass wir damals auf dem richtigen Weg waren.
Konstruktion und Bau der Rumpfform
Um eine makellos glatte Oberfläche des fertigen Bootes ohne viel nachträgliche Spachtel- und Schleifarbeit zu erhalten, haben wir fast ausschließlich mit Negativformen gearbeitet. Im Spantenriss wurden die Spanten und der Spiegel mit den Zuschlägen für die Längs- spanten und die Hartfaserplatte aufgezeich- net und dabei wurde so genau gearbeitet, dass wir die Toleranzen der Vermessung zu unseren Gunsten, dh. Regattaschnelligkeit, ausgenutzt haben. Mutig - aber erfolgreich - wie sich später herausstellte. Die Form war in der Längsachse teilbar. Wir befürchteten, den Rumpf ohne Zerstörung der Form nicht ausformen zu können. Nicht unbedingt erforderlich, wie wir später feststellten.
Aufbau der Rumpfform mit Längsspanten
A
lle Spanten wurden verleimt und verschraubt, um sicher zu sein, die Form häufig nutzen zu können. Die provisorischen „Decksbalken“ sorgten für eine starre, verwindungssteife Form während des Aufbaus. Bei der Herstellung der Längsspanten aus abgelagertem Fichtenholz achteten wir auf exakte Maßhaltigkeit. Wir strebten ein Ober- flächenfinish wie in der Autoindustrie an. Hilfreich war, dass das Institut für Schiffbau im Keller des Audimax eine voll ausgestattete Schreinerwerkstatt unterhielt, in der ein Schreinermeister für Ordnung und scharfe Werkzeuge sorgte. Dass im Fahrradkeller gleich nebenan Platz für die Aufstellung der Formen war, war ein weiterer Glücksfall. Fahrräder wurden damals, auch bei Studenten, mangels Klimakatastrophe kaum genutzt.
Einbau der Hartfaserplatten
Auf die Längsspanten wurden dann die Hartfaserplatten verleimt und verschraubt, die Übergänge 10 mal mit Polyesterspachtel gespachtelt und geschliffen, danach wurde die Beschichtung der Rumpfform mit DD-Lack mit der Spritzpistole in 10 Schichten aufgetragen und jedesmal geschliffen. Eine kraftraubende und langwierige Arbeit. Der Lampentest zeigte jede winzige Unebenheit im spiegelnden Lack.
Bau der Decksform
Ebenso wie die Rumpfform wurde die Decksform aus dem Spantenriss abgeleitet. Der Aufbau erfolgte ebenso wie der Rumpfaufbau. Der Konstrukteur des Zugvogels hat den Riss ohne dreidimensionale Wölbungen gestaltet, so dass das Aufbringen der Hartfaserplatten ohne Verspannungen möglich war. Auf den nebenstehenden Fotos wird unsere Arbeit von einem späteren ASV‘er begutachtet.
Arbeitsschritte bei der Herstellung der Decksform
Auch bei der Decksform war auf eine formstabile Herstellung zu achten, um den späteren Zusammenbau von Rumpf und Deck problemlos gestalten zu können. Hier wurde dem Oberflächenfinish noch mehr Sorgfalt gewidmet. Um rutschreduzierende Flächen auf Deck und dem Cockpitboden zu erzeugen, wurden vor dem Lackieren Rauhfasertapetenflächen aufgeklebt.
Die Schwertkastenform
Die Schwertkastenform haben wir in der Schreinerwerkstatt auf der Hobelbank aufgebaut. Sie war die einzige Positivform von insgesamt 14 notwendigen Formen für:
- Rumpf
- Deck
- Schwertkasten
- Schwertkastendeckel
- Cockpit
- 4 Lukendeckel für die Cockpitwände
- Runddeckel im Cockpitboden
- Reitbalken
- Ruderkopf
- Ruderblatt
- Zwischenboden im Vorschiff
Aufbringen des Gelcoats
Das farbige Gelcoat (RAL3000), damals eine beliebte Farbe, wurde mit einer Rolle in die sorgfältig vorbereitete Form eingebracht, mit Polyesterflies abgedeckt, um die Abriebfestigkeit zu erhöhen, und dieses danach wieder mit Gelcoat überrollt.
Die Formvorbereitung:
- mehrfaches Auftragen von Bohnerwachs
- jeweiliges Polieren nach dem Auftragen
- Auftragen von Propylalkohollack
Der acetonfeste aber wasserlösliche Lack sollte das Ausformen durch Einleiten von Wasser zwischen Rumpf und Deck in hartnäckigen Fällen ermöglichen. Dank intensiver Wachs- und Polierarbeit war diese Prozedur aber nicht nötig.
Aufbau des Glasfaserlaminates
Die Außenschicht des Rumpf- und Schwert- kastensandwiches, aufgebaut aus einem Gewebe und mehreren Lagen Glasfaser- matten, die nass in nass verarbeitet wurden. Die zugeschnittenen und mit Polyester spritzbeschichteten PVC-Platten wurden in die feuchte Laminatschicht gedrückt. Der Druck musste bis zur Aushärtung bestehen bleiben.
Anpressen der PVC-Schaumplatten
Die Seitenwandplatten wurden unter Nutzung des Hebelprinzips mit Latten und Schraubzwingen angepresst. Für das Anpressen der Bodenplatten ergab sich eine einfache Lösung. Vor dem Eingang zum „Fahrradkeller“ wurde gerade der Bürgersteig neu aufgebaut. Die gestapelten Gehwegplatten waren als Gewichte zum Anpressen der PVC- Schaumplatten gut geeignet.
Bei später gebauten Booten, der Bürgersteig war inzwischen fertig geworden, konnte das Anpressen mittels einer Folie und einer Vielzahl von ausge- liehenen Vacuumpumpen erreicht werden. Das Ergebnis war wesentlich besser als das Verfahren mit den Betonplatten.
Der ausgeformte Rumpf
Hier liegt der ausgeformte Rumpf neben der Form. Für alle weiteren Arbeitsschritte musste der Rumpf wieder in die Form eingelegt werden, um ein Verwinden des labilen Rumpfes zu vermeiden.
Einbau der Spanten
Für eine Erhöhung der Rumpffestigkeit und als Auflage für das Cockpit wurden Spanten aus PVC-Platten ausgeschnitten mit Wasserdurchlauföffnungen versehen und in den Rumpf eingeklebt.
Überlaminieren der Schaumstoffspanten
Um eine exakte Auflage des Cockpits sicherzustellen, wurden auch die Spantenmaße aus dem Spantenriss übernommen. Die Schaumstoffspanten wurden mit Polyester angeklebt, mit Steinen angepresst und danach mit einem Glasfaserlaminat überzogen.
Spanteneinbau unter Deck
Um die Begehfestigkeit zu erhöhen, wurde auch das Deck wie der Rumpf mit Spanten versehen. Zwei im Winkel gegeneinander geneigte Schaumstoffstreifen verhindern bei hoher Belastung ein Verwinden der Spanten.
Bau und Einbau des Cockpits
Das über eine Form laminierte Cockpit bekam somit eine makellose sichtbare Oberfläche.
Die hier zu sehenden roten Farbflächen waren anhaftende Rückstände des Polypropylalkohols.
Kein Problem, da wasserlöslich.
Die Aussteifungen durch den Verbund von Rumpf, Spanten, Schwertkasten, Cockpit und das hier noch fehlende Deck sorgten für eine sehr hohe Festigkeit und Verwindungssteifigkeit des Bootes.
Die Hochzeit von Rumpf und Deck
Unter dem Druck von 120 Schraubzwingen, geliehen in verschiedenen Hochschulinstituten, wurden Rumpf und Deck, jeweils in die Formen eingelegt, mit Polyester und zwischengelegten getränkten Glasfasermatten wasserdicht miteinander verbunden.
Für eine sichere Verbindung des Decks mit dem Cockpit und dem Schwertkastenkopf an der Mastfußauflage sorgte das Gewicht von mehreren Betonplatten.
Aushärten des Polyesterharzes
Um ein sicheres Aushärten zu gewährleisten, sorgten Heizlüfter unter einer Abdeckfolie für ausreichende Reaktionswärme.
Das Boot ist fast fertig aber schon transportbereit
Das transportbereite Boot vor dem Audimax in der Wüllnerstraße.
Auf dem Wildenhof in Woffelsbach am Rursee werden die Beschläge montiert und das Boot aufgeriggt.
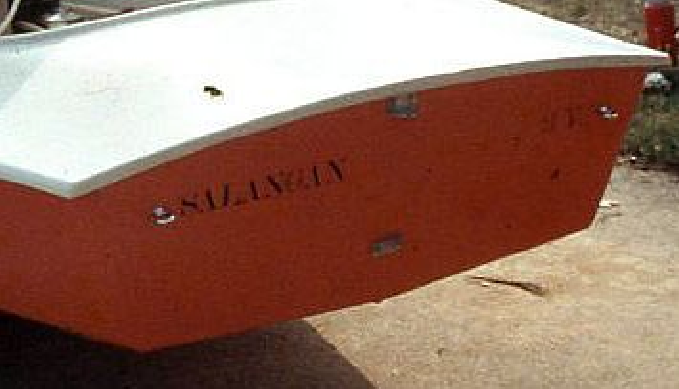
Die letzten Komplettierungsarbeiten sind abgeschlossen
Nachdem alle Beschläge montiert und das stehende und laufende Gut installiert sind, kam der große Augenblick, auf den wir nach einjähriger Bauzeit mit großer Spannung gewartet hatten.
Schwimmt das Schiff? Segelt es ordentlich? Hat es bei Regatten eine Chance?
Nach der Taufe wird es sich allmählich herausstellen.
Aus heutiger Sicht kann man sagen:
Mit diesem Schiff waren hochrangige Regatten zu gewinnen. Das ist bewiesen.
Taufe auf den Namen Salangan
Nach der Taufe waren viele Hände behilflich „Salangan“ über unwegsames Gelände in Dienst zu stellen.
Die Indienststellung
Über eine steile Uferböschung wird Salangan seinem Element übergeben. Im Vordergrund die beiden glücklichen Erbauer.
Es schwimmt und es segelt sogar
Der erste Wasserkontakt verlief problemlos. Unser erster Segelschlag war ein unvergessliches Erlebnis.
Mehr als 40 Jahre später liegt Salangan wieder am Steg des ASV zur Nutzung durch die Mitglieder.
Mein Freund Hans Schlott lebt leider nicht mehr.
Es würde uns beide freuen, wenn die Aktiven des ASV Salangan weiterhin pfleglich behandelten.
Klaus Hannes